Zgrzew dwóch rur jest najbardziej zawodnym odcinkiem rurociągu. To, jak długo wytrzyma żyłka, zależy od jej jakości. Aby uniknąć wypadków podczas eksploatacji konstrukcji, przeprowadza się wykrywanie wad rurociągów. Jest to szczególnie ważne w przypadku autostrad położonych pod ziemią.
Informacje ogólne
Istnieje kilka metod wykrywania wad spawów rur:
- magnetyczny;
- akustycznie;
- elektryczny;
- optyczny.
Ich zadaniem jest określenie szczelności połączeń, wytrzymałości metalu w szwach, czy występują naprężenia i inne parametry, które decydują o niezawodności rurociągów. Jednocześnie metody wykrywania wad są prawie takie same dla wszystkich rodzajów sieci: ciepłowniczych, gazowych, wodnych, ropociągowych.
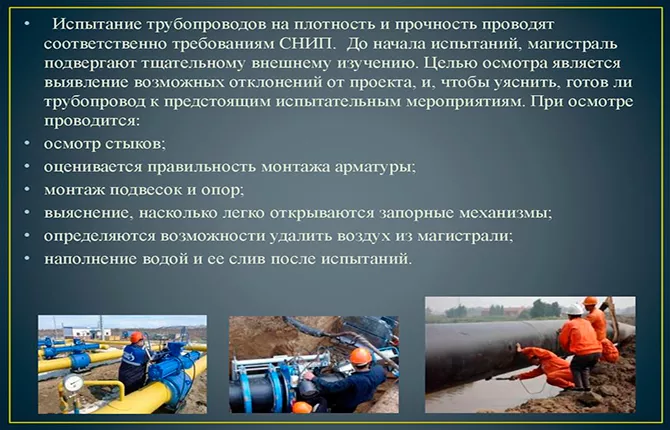
Wszystkie wyżej wymienione metody należą do kategorii technologii "nieniszczących" . Oznacza to, że wykrywanie wad odbywa się bezpośrednio na placu budowy. Połączenia rur nie ulegają zniszczeniu, co zmniejsza koszty prac instalacyjnych.
Wykrywanie wad rurociągów opiera się na skanerze zwanym defektoskopem. Każda technologia ma swoją własną zasadę działania tego sprzętu. Najbardziej wydajne defektoskopy:
- prądy wirowe;
- ultradźwiękowy;
- puder magnetyczny;
- kapilara.
Szczegóły dotyczące metod
Wykrywanie wad rurociągów to procedura, którą należy wykonać po zamontowaniu rurociągu. Pozwoli to uniknąć jego ewentualnego zniszczenia podczas eksploatacji. Wykrywanie wad umożliwia wykrycie wszelkich defektów w rurach. Zasada działania skanerów wykorzystywanych w procesie diagnostycznym jest inna. Dlatego warto najpierw dokładniej przestudiować każdy z nich.
Defektoskopy wiroprądowe
Zasada działania urządzenia polega na wytwarzaniu prądów wirowych, które są kierowane z zewnętrznej płaszczyzny rurociągu do wewnętrznej przez spoinę. Prąd przepływający przez jednorodną strukturę metalową nie zmienia swoich parametrów. Jeśli wewnątrz szwu występują defekty, to znaczy jego jednolitość jest zerwana, opór wzrasta, co zmniejsza siłę prądu wirowego.
Defektoskop naprawia i rozszyfrowuje ten spadek, określając jakość metalu spoiny, defekty i niejednorodność.
Zalety metody:
- duże tempo pracy;
- niski błąd wyniku;
- niski koszt operacji.
Wady:
- grubość badanego szwu - nie więcej niż 2 mm;
- niezawodność urządzenia jest niska.
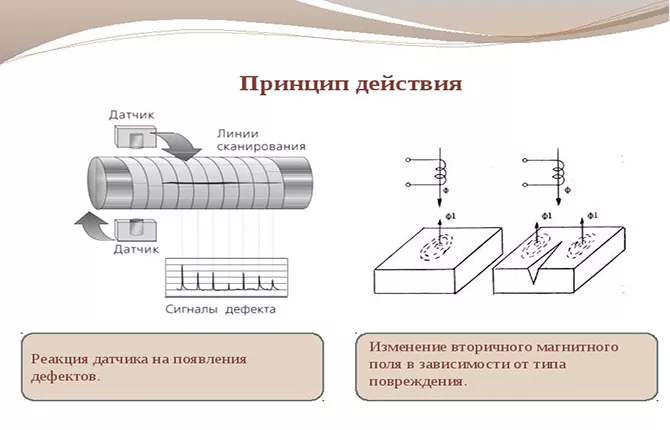
Defektoskopy ultradźwiękowe
Badania ultradźwiękowe rurociągów są uważane za najczęściej stosowaną technologię. Przeprowadza się ją za pomocą pięciu różnych metod wykrywania wad:
- Metoda echa impulsowego.
- Cień.
- Echo Lustra.
- Lustro-cień.
- Metoda delta.
W pierwszym przypadku ultradźwięki są wysyłane przez instrument przez warstwę spoiny. Jeśli wewnątrz metalu występują defekty, impuls odbija się w postaci echa. Oznacza to, że ultradźwięki powracają. Urządzenie rejestruje czas powrotu, który określa głębokość otoczki lub porów.
W drugim przypadku stosuje się nie tylko urządzenie wysyłające sygnał ultradźwiękowy, ale także reflektor. Ten ostatni jest instalowany po przeciwnej stronie złącza spawanego rurociągu. Jeśli znana jest odległość między dwiema częściami urządzenia oraz czas propagacji dźwięku, to zmieniając drugi parametr (powiększenie) można określić, gdzie znajduje się usterka, jaka jest jej wielkość.
Trzecia wersja defektoskopii ultradźwiękowej przypomina pierwszą.Jedynie defektoskop wyposażony jest w reflektor, który montowany jest na górnej powierzchni szwu oraz emiter sygnału. Oba elementy są do siebie równoległe. Jeśli sygnał dotarł do odbiornika, oznacza to, że wewnątrz metalu odbijającego wiązkę jest defekt.
Następna metoda jest podobna do poprzedniej. Różnica polega na tym, że sygnalizator i reflektor są ustawione względem siebie pod kątem 90°.
Piąta metoda defektoskopii ultradźwiękowej jest rzadko stosowana. Powodem jest złożoność konfiguracji sprzętu, długie dekodowanie wyników. Polega na przekierowaniu energii ultradźwiękowej, której kierunek zmienia defekt spoiny.
W tym przypadku dostarczana jest belka poprzeczna, przechodząca w belkę podłużną. Częściowo występuje odbicie lustrzane. Odbłyśnik wychwytuje dokładnie sygnał podłużny, którego siła określa wielkość skazy w stali.
Defektoskopy cząstek magnetycznych
To wykrywanie defektów opiera się na właściwościach stali do zmiany pola magnetycznego w pobliżu obszarów, które różnią się od głównej części niską gęstością. Tutaj staje się słabszy. Pęknięcia, ubytki lub pory wewnątrz metalu mają małą gęstość ze względu na znajdujące się w nich powietrze.
Proszek magnetyczny, zwany też ferromagnetykiem, służy do wykrywania defektów w rurociągach. Wlewa się go na spoinę, gdzie prąd elektryczny jest dostarczany za pomocą dwóch cewek - magnesującej i dodatkowej. Elektryczność wewnątrz metalu tworzy pole magnetyczne. Jeśli obecne są defekty, osłabia się wokół nich. To jest powód przyciągania proszku magnetycznego.
Jeżeli podczas badania na powierzchni zbierze się proszek, świadczy to o jednym - w tym miejscu stwierdzono wadę spoiny. W ten sposób przeprowadza się wykrywanie wad głównych rurociągów.
Istnieją dwie opcje testowania - na sucho i na mokro. W pierwszym przypadku stosuje się proszek magnetyczny. W drugim zawiesina tego proszku jest roztworem wodnym.
Aby jakość kontroli przeprowadzonej w drugim wariancie była wysoka, konieczne jest dodatkowe potraktowanie badanej powierzchni materiałem pośrednim – olejem technicznym, smarem i innymi.
Zaletami badania magnetyczno-proszkowego są:
- efekt wizualny, widoczny bez dodatkowych urządzeń;
- niska cena.
Wady:
- mała głębokość badania - do 1,5 mm;
- można stosować tylko na rurociągach zmontowanych ze stopów ferromagnetycznych;
- trudność w rozmagnesowaniu dużych rur.
Defektoskopy kapilarne
Ta technologia służy do wykrywania małych pęknięć powierzchniowych, które nie są widoczne gołym okiem. Potwierdzają, że metal na styku dwóch odcinków rurociągu nie jest jednorodny.
Proces wykrywania wad rurociągu przebiega następująco:
- Na spoinę nakłada się substancję wskaźnikową, penetrant. Pod wpływem sił kapilarnych ma tendencję do wnikania w najmniejsze defekty. Stąd nazwa metody.
- Poddana obróbce powierzchnia zostaje oczyszczona z nałożonej substancji, która wniknęła już głęboko w metal.
- Aplikuje się na nią wywoływacz w postaci białego pudru. Może to być talk, tlenek magnezu lub inna substancja. Ma ważną właściwość - adsorpcję. Oznacza to, że może wchłaniać inne substancje.
- Wywoływacz zaczyna wyciągać penetrant ze szczelin, który tworzy wzór spoin na powierzchni białego proszku. Jednocześnie wskaźnik jest dobrze widoczny w promieniach ultrafioletowych.
Ten typ defektoskopii rurociągów jest zwykle stosowany, jeśli konieczne jest wykrycie defektów powierzchniowych w metalu na złączu. W przypadku głębokich ubytków jest to bezużyteczne. I to jest minus. Główną zaletą jest łatwość wdrożenia.
Wyniki
Do sprawdzenia połączeń rurowych w głównych rurociągach nie jest konieczne stosowanie jednej metody wykrywania wad. Każdą witrynę można zbadać w taki czy inny sposób. Wybierając optymalną metodę, należy najpierw ocenić, w jaki sposób odpowiada jej staw. Na przykład metoda kapilarna jest odpowiednia dla rurociągów wodnych, a tylko metoda ultradźwiękowa dla rurociągów naftowych i gazowych.
Wykrywanie wad rurociągów to niezbędna procedura, która pozwala ocenić jakość układanego rurociągu, zidentyfikować wszystkie możliwe wady. Przeprowadza się go na kilka sposobów. Zabieg lepiej wykonać na etapie montażu rurociągu, aby po zakończeniu prac nie napotkać przykrych „niespodzianek” w postaci nieszczelności czy pęknięć.
Której metody wolisz użyć i dlaczego? Napisz w komentarzach. Udostępnij artykuł w sieciach społecznościowych i dodaj go do zakładek, aby nie stracić przydatnych informacji.
Zalecamy również obejrzenie wybranych filmów na nasz temat.
Diagnostyka odcinka liniowego rurociągów głównych.
Jak wygląda kontrola rentgenowska spoin w produkcji.