Konstrukcja długich rurociągów wymaga licznych połączeń spawanych poszczególnych rur. Jakość spawania może mieć znaczący wpływ na wydajność całej autostrady. Metody kontroli złączy spawanych umożliwiają mówienie z wystarczającą pewnością o ich jakości.
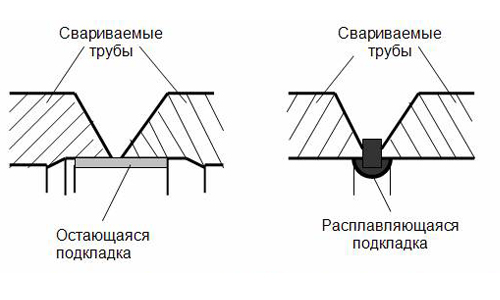
Schemat montażu połączeń rur przez spawanie.
Standardy rządowe ściśle regulują potrzebę weryfikacji niezawodności rurociągów. Taka weryfikacja jest konieczna do zapewnienia bezpieczeństwa ich usług. Nieniszczące badania połączeń spawanych rur są objęte obiektywnym systemem kontroli jakości autostrad i są obowiązkowym i skutecznym sposobem oceny ich niezawodności i bezpieczeństwa.
Tworzenie defektów
Podczas spawania rurociągów i odpowiadających im efektów termicznych w spoinie i obszarach do niej przylegających mogą powstać wady (pęknięcia).
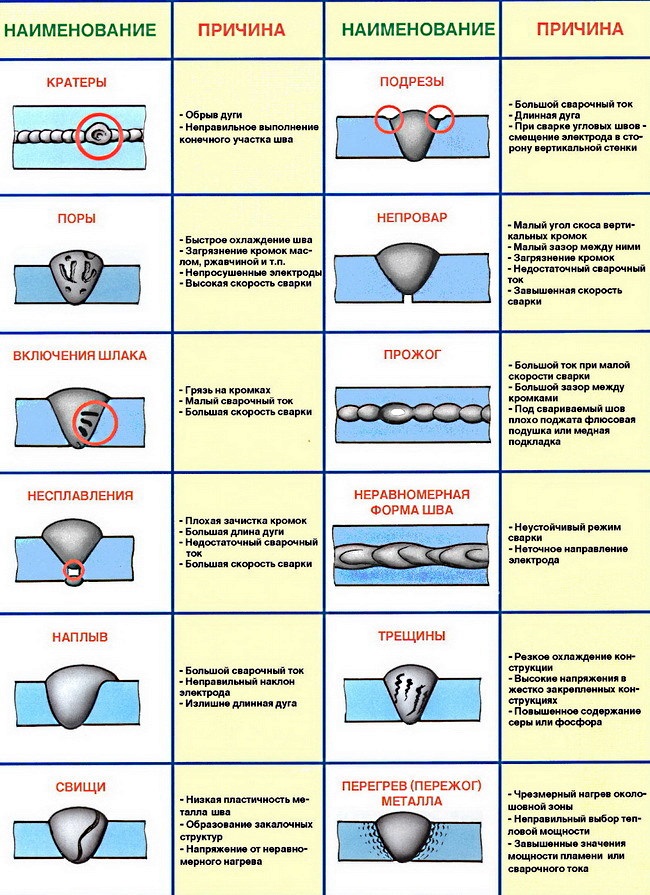
Wady spoiny
Te wady podczas pracy mogą prowadzić do zmniejszenia właściwości wytrzymałościowych metalu, zmniejszenia niezawodności i trwałości rurociągu, zmian właściwości transportowych, niedostatecznej dokładności wymiarów i pogorszenia wyglądu. Głównymi przyczynami wad są: naruszenia technologii spawania, użycie materiałów niskiej jakości lub niewystarczające kwalifikacje pracownika. Szereg defektów połączeń spawanych jest zauważalnych przez kontrolę wzrokową, ale większość z nich jest ukryta i może być wykryta tylko specjalnymi metodami. Innymi słowy, wady mogą być wewnętrzne i powierzchniowe (zewnętrzne).
Rodzaje uszkodzeń i wad
Można wyróżnić główne formy defektów w strefach spawanych: napływ masy, podcięcie, nierówna penetracja, pęknięcia i pory (zarówno zewnętrzne, jak i wewnętrzne), wtrącenia obce.
Wady można podzielić i ze względu na ich występowanie. Wyróżnia się dwie główne grupy: wady spowodowane cechami metalurgicznymi i efektami termicznymi oraz wady spowodowane czynnikami ludzkimi, naruszenie warunków spawania. Pierwszą z nich można przypisać strukturze kryształu - pęknięciom (zimnym i gorącym) w spoinie i przekroju szwu, porom, żużlowi, zmianom strukturalnym w metalu. Z drugiej grupy, takie defekty jak nienormalizowane wymiary spoiny, nierówna penetracja, podcięcia, przepalenia, guzki, kratery, niewypełniony metal i inne wyróżniają się.
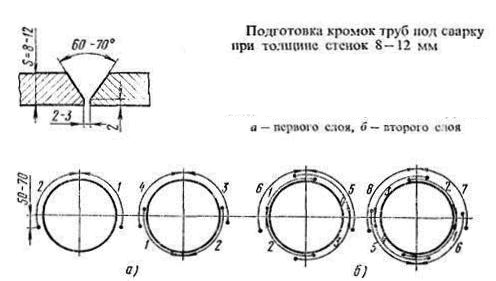
Schemat przygotowania krawędzi rury do spawania.
Naruszenie rozmiarów szwu może mieć wpływ na niezawodność rurociągów, więc jeśli takie odchylenia są większe niż znormalizowane przez normy, uważa się je za wady. Takie wady pośrednio wskazują na obecność defektów wewnętrznych w spoinie. Głównymi wadami tego typu są: ostre nierówności szerokości i wysokości spoiny wzdłuż jej długości, strome przejście ze strefy spawania wstępnego do spoiny, zauważalna szorstkość stopiwa, duże siodełka i talia.
Rurociągi: analiza różnych defektów
Wada spawanego złącza w postaci przelewu pojawia się, gdy stopiwo silnie przecieka na zimną strefę bliską szwu. Żagle mogą mieć postać pojedynczych kropelek i mogą osiągnąć znaczną odległość wzdłuż szwu spawalniczego. Przyczyny zwiotczenia:
- nadmiar prądu spawania;
- niewłaściwe nachylenie;
- ruch elektrody podczas spawania;
- ignorując kąt rur, gdy są połączone.
Spadaniu często towarzyszy pojawienie się nierównej i słabej jakości penetracji metalu spoiny, a także pojawienie się zewnętrznych i wewnętrznych pęknięć.
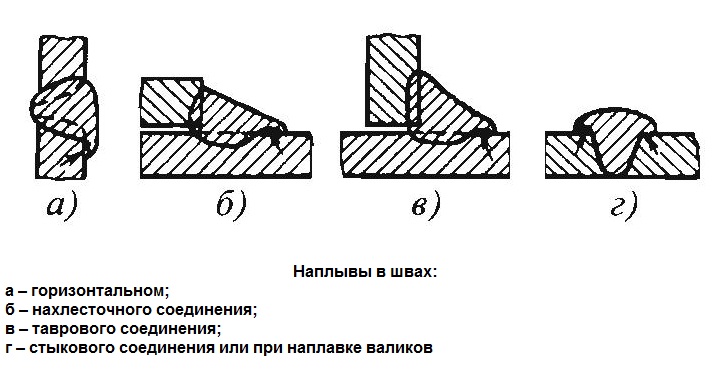
Schematy tworzenia guzków.
Podcięcia to rowki w metalu, które pojawiają się na granicy ze spoiną. Taka wada zmniejsza rzeczywisty przekrój szwu i prowadzi do pojawienia się nadmiernych naprężeń, które mogą prowadzić do ich wzrostu w pęknięcia z następczym zniszczeniem złącza spawanego.
Wady w postaci przepalenia pojawiają się jako dziury, przez które roztopiony płyn wypłynął z jeziorka spawalniczego. Powodem powstawania takiej wady może być niska prędkość spawania, przeszacowana szczelina między końcami rur, gdy są one zgrzewane, a wytrzymałość prądu spawania jest przekroczona. Niewystarczająca lub nierówna penetracja szwów jest spowodowana brakiem niezawodnego połączenia krawędzi na małych obszarach. Taka wada zmniejsza rzeczywisty przekrój spoiny i prowadzi do pojawienia się naprężeń szczątkowych, które mogą powodować późniejsze pękanie i niszczenie metalu.
Pęknięcia można przypisać najbardziej niebezpiecznym rodzajom wad. Mogą pojawić się w dowolnym punkcie strefy spawania (w tym w pobliżu metalowego obszaru metalu) i mieć dowolny kierunek (wzdłużny i poprzeczny). Ze względu na swój rozmiar są one podzielone na mikropęknięcia i pęknięcia. Taka wada jest spowodowana zarówno przez niewłaściwe warunki krystalizacji stopu, jak i przez nadmiar stężenia węgla, siarki i fosforu w jeziorku spawalniczym. Pęknięcia znacząco wpływają na wszystkie główne parametry złączy spawanych rurociągów.
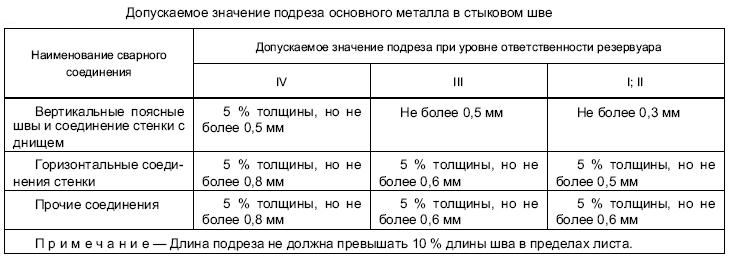
Tabela dopuszczalnych wartości podcięcia podczas spawania.
Wtrącenia obce osłabiają właściwości wytrzymałościowe. Najbardziej niebezpieczna jest obecność wtrąceń żużla utworzonych, gdy po spawaniu nie ma wystarczającego oczyszczenia żużla z powierzchni spawów. Wtrącenia te znacznie przyspieszają korozję metalu.
Pory gazu lub powietrza są zwykle tworzone wewnątrz spoiny. Mogą mieć pojedynczy charakter i mogą pochodzić z grup, a nawet tworzyć łańcuchy pustek. Pory mogą osiadać na powierzchni metalu, tworząc wgłębienia (przetoki). Pory znacznie zmniejszają wytrzymałość szwów, a tworzenie łańcuchów pustych przestrzeni może spowodować obniżenie ciśnienia rurociągu.
Naruszenie struktury metalu spoiny lub strefy niemal bez szwu może objawiać się wzrostem stężenia tlenków, mikroporów i mikropęknięć, gruboziarnistego ziarna. Reżim termiczny w tworzeniu struktury metalu odgrywa kluczową rolę. Nadmierne ogrzewanie prowadzi do powstawania dużych ziaren w strukturze. Po spaleniu metalu mogą pojawić się ziarna z utlenionymi powierzchniami. Wszystko to prowadzi do kruchości metalu.
Ogólna teoria badań nieniszczących
W metodzie badań nieniszczących znajduje się zestaw metod, które pozwalają określić wymagane parametry bez narażania integralności złącza spawanego rurociągu. Połączenia spawane muszą być monitorowane na wszystkich etapach przygotowania, produkcji i przygotowania do pracy oraz okresowo podczas pracy.
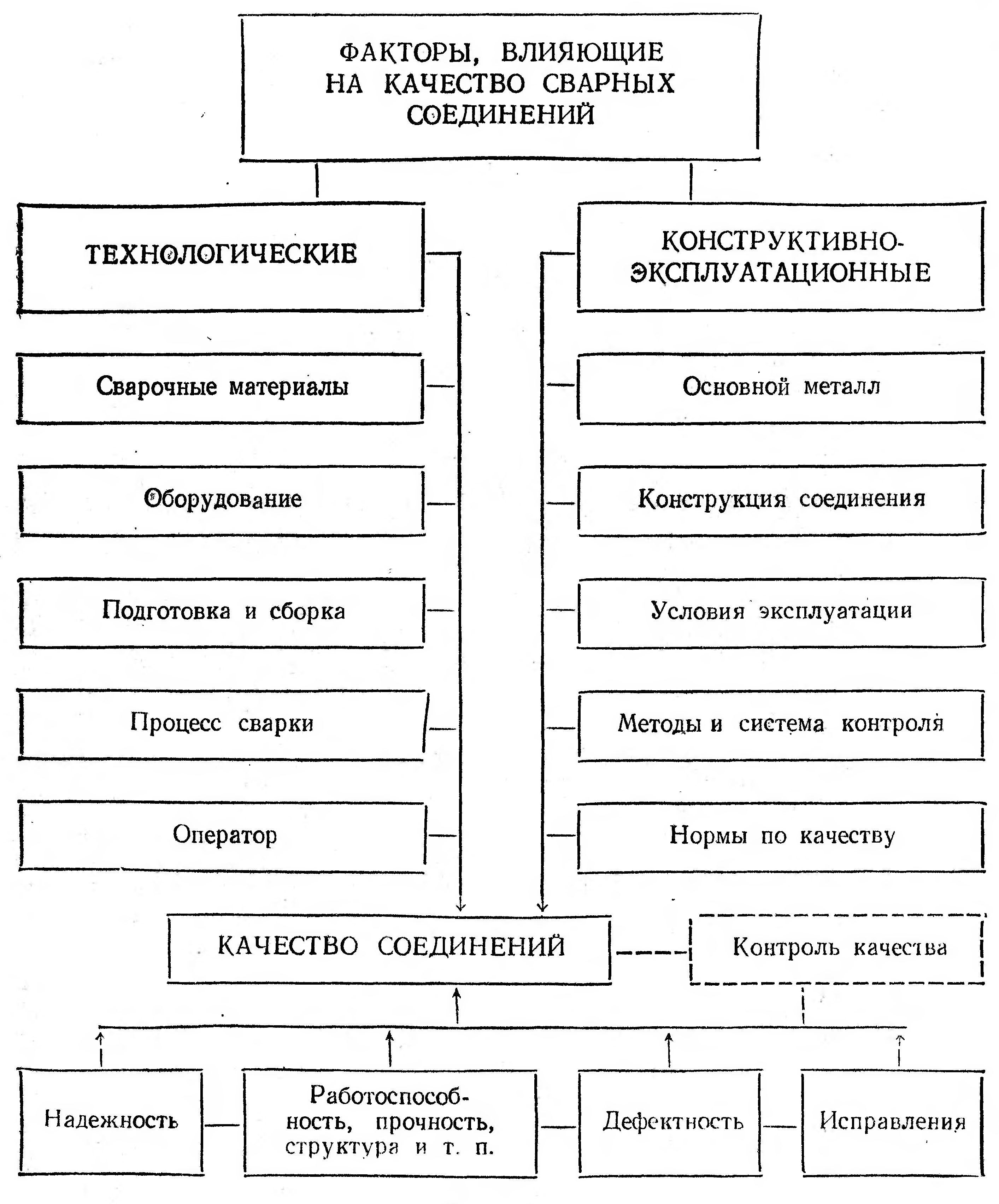
Czynniki wpływające na jakość spoin.
Metody kontroli nieniszczącej łączą kontrolę za pomocą badania zewnętrznego w celu wykrycia defektów zewnętrznych, badają szczelność spawów połączeń spawanych oraz metody sterowania w celu ustalenia ukrytych wad za pomocą specjalnych urządzeń. Badania nieniszczące są przydzielane jako odrębny etap procesu technologicznego wytwarzania całego rurociągu.
Normy stanowe ściśle regulują kontrolę połączeń spawanych rurociągów. Tak więc GOST 3242-79 definiuje sześć podstawowych typów sterowania, a GOST 30242-97 klasyfikuje typy defektów w połączeniach spawanych rurociągów. Głównym celem stosowania specjalnych metod jest określenie lokalizacji i rozmiaru ukrytych defektów, więc wszystkie techniki należą do grupy wykrywania wad. System badań nieniszczących obejmuje następujące metody: kapilary, promieniowanie, akustyczne, magnetyczne, ultradźwiękowe.
Zewnętrzna kontrola wizualna
Pierwszą metodą nieniszczących badań złączy spawanych rurociągów jest zewnętrzna kontrola wzrokowa i pomiary, które są przeprowadzane w sposób ciągły na wszystkich etapach produkcji i eksploatacji rurociągów. Przede wszystkim, poprzez wizualną kontrolę złącza spawanego rur, określana jest obecność wad zewnętrznych, takich jak przelewy, podcięcia, kratery porów, przepalenia, pęknięcia zewnętrzne i inne. Przy tej kontroli zaleca się stosowanie szkła powiększającego z dziesięciokrotnym wzrostem.
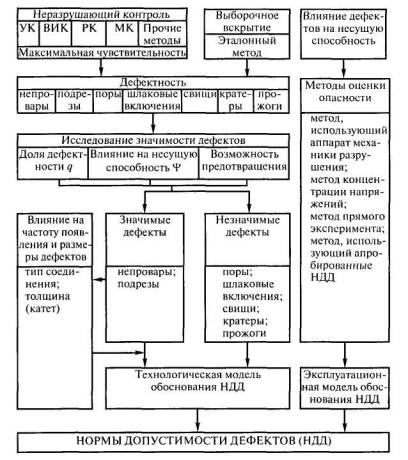
Ogólny schemat uzasadnienia norm dopuszczalności wad.
Następnym krokiem jest zmierzenie wymiarów spawanych elementów i ustalenie lokalizacji defektów. Podczas pomiaru ustalane są następujące wymiary spoiny: jej szerokość i wysokość, rozmiar części wypukłych i narożniki na granicy ze strefą bliską szwu. Do kontroli rozmiarów używane są specjalne szablony. Wyniki pomiarów spoiny są porównywane ze znormalizowanymi wartościami ustalonymi przez normy państwowe dla tego rodzaju spawania.
Test szczelności
Spawane połączenia rur muszą być szczelne dla tych substancji (cieczy lub gazów), które są transportowane przez ten rurociąg. Kontrola szczelności (nieprzepuszczalność) jest przeprowadzana po zmontowaniu rurociągu. Obejmuje następujące podstawowe metody weryfikacji: kapilarne, chemiczne, bąbelkowe, a także poprzez odkurzanie i używanie wykrywacza wycieków.
Kontrola złączy spawanych metodą kapilarną opiera się na właściwości nafty do stosowania kapilar do penetracji przez puste przestrzenie (pory, pęknięcia). Aby sprawdzić szczelność spoiny, stosuje się wodny roztwór kredy i suszy. Od strony szwu naprzeciwko powierzchni pomalowanej kredą powierzchnia jest obficie podlewana naftą. W przypadku wycieku na kredowej powierzchni pojawią się ślady nafty. Przy stosowaniu nafty możliwe będzie określenie obecności defektów wewnętrznych o rozmiarze mniejszym niż 0, 1 mm.
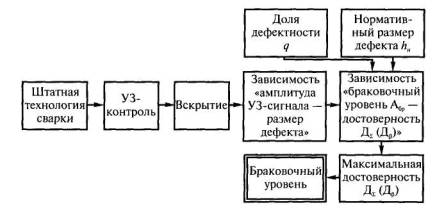
Schemat wyboru poziomu odrzucenia za pomocą ultradźwiękowych badań szwów czołowych.
Kontrola szczelności przy użyciu amoniaku opiera się na barwieniu wskaźnika w kontakcie z alkaliami. Wskaźnik jest roztworem fenoloftaleiny lub rtęci z kwasem azotowym, odczynnikiem jest amoniak w stanie gazowym.
Metoda kontroli pęcherzyków obejmuje sprawdzenie ciśnienia powietrza. Sprężone powietrze jest pompowane do rury, a szczelność spoiny jest sprawdzana przez pęcherzyki, gdy sekcja rurociągu jest zanurzona w kąpieli wodnej. Test może opierać się na wykrywaniu pęcherzyków wody podczas tworzenia ciśnienia hydraulicznego wewnątrz rury. Przed badaniem powierzchnia rury jest osuszana, a podczas testów zapewniane jest wewnętrzne ciśnienie wody, które przekracza 1, 5-krotne ciśnienie robocze w rurociągu.
Podczas przeprowadzania kontroli złączy spawanych krytycznych rurociągów stosuje się sterowanie za pomocą gazoelektrycznego wykrywacza wycieków. Do testowania stosuje się gazowy hel, który ma wysoką przepuszczalność. Specjalna sonda do wykrywania wycieków wykrywa wygląd gazu, a jednostka elektroniczna analizuje jego ilość i stopień szczelności spoiny.
Metoda instalacji defektów magnetycznych
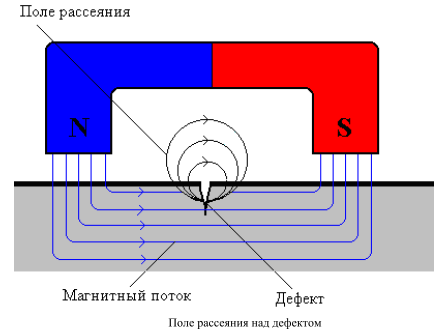
Schemat magnetycznej metody kontroli jakości spoiny.
Metody badań nieniszczących połączeń spawanych rurociągów, uwzględniające właściwości magnetyczne materiałów, umożliwiają określenie lokalizacji defektów poprzez badanie rozpraszania magnetycznego w niejednorodnych strukturach podczas namagnesowania metalu strefy spawanej. Część rury jest namagnesowana za pomocą solenoidu umieszczonego w wewnętrznej wnęce lub przez nawijanie drutu nawijającego na szew spawalniczy. Badanie przeprowadza się metodą proszkową, indukcyjną lub magnetograficzną, które różnią się sposobem pomiaru rozproszenia strumienia magnetycznego.
Metoda kontroli proszku polega na użyciu proszku magnetycznego (opiłki żelaza) osadzonego na powierzchni spawanego obszaru. Gdy pole magnetyczne powstaje w proszku, cząstki są zorientowane i obraz widma magnetycznego jest wyraźnie utworzony. Dzięki temu można wykrywać pęknięcia i pory na znacznych głębokościach. Aby sterować za pomocą metody indukcyjnej, poszukiwacze są wykorzystywani, w których siła elektromotoryczna jest wytwarzana pod wpływem rozpraszającego strumienia magnetycznego. W takim przypadku emitowany jest sygnał dźwiękowy lub pojawia się sygnał świetlny. Metoda sterowania magnetograficznego umożliwia rejestrowanie przepływu dyspersji na taśmie magnetycznej umieszczonej na powierzchni złącza spawanego. Stosując defektoskop magnetyczny, obecność defektów określa się przez porównanie wyników uzyskanych z normą.
Metoda promieniowania
Nieniszczące metody kontroli połączeń spawanych rurociągów opierają się na właściwościach promieniowania rentgenowskiego i gamma. Metal pochłania promieniowanie inaczej w obecności wad lub zmian strukturalnych, które uwzględniają tę metodę weryfikacji. Spoiny są penetrowane przez promienie za pomocą specjalnych źródeł promieniowania. Promienie są mocowane na specjalnej folii, gdzie obszary ciemnienia wskazują na obecność defektów. Lokalizacja i ich rozmiary są łatwo rozpoznawalne. Źródłami promieniowania są powszechnie stosowane urządzenia RUP 150-1 i RUE 120-5-1.
Procedura testowa jest podobna do kontroli rentgenowskiej. Penetracyjna zdolność promieni gamma jest wyższa niż promieni rentgenowskich, co zwiększa możliwości radiacyjnej metody kontroli spawanych złączy.
Metoda ultradźwiękowa
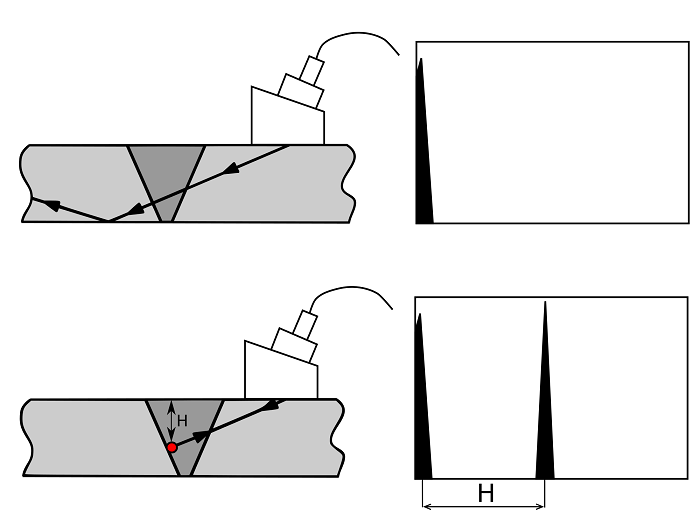
Kontrola ultradźwiękowa spoin.
Nieniszcząca ultradźwiękowa metoda kontroli połączeń spawanych jest powszechnie stosowana do ustalania defektów w masie metali. Ta metoda wykorzystuje właściwości fal ultradźwiękowych do penetracji materiału na znaczną głębokość i rozproszenia na granicach wad. Źródłem fali jest piezocrystal umieszczony na specjalnej płytce (sondzie).
Ultradźwięki są stosowane pod innym kątem od 40 do 73 ° C, aby zapewnić pełny obraz. Inna płyta urządzenia rejestruje odbite fale. Najczęściej stosowaną metodą ultradźwiękową jest metoda echa, w której urządzenie rejestruje bezpośrednie odbicie impulsu z defektu (echa). Podczas przeprowadzania kontroli połączeń spawanych rurociągów stosowane są defektoskopy ultradźwiękowe typu TUD-320 lub TUD-310. Ponadto stosowane są metody wykrywania wad ultradźwiękowych w cieniu i cieniu.
Przyrządy i urządzenia zalecane do nieniszczących badań spoin rurociągów:
- lupa;
- zacisk;
- mikrometr;
- wskaźnik głębokości;
- wzory spoin;
- Rentgenowskie, radiacyjne, ultradźwiękowe i magnetyczne defektoskopy;
- wskaźnik wycieku;
- analizator gazu.
Nieniszcząca analiza połączeń spawanych rurociągów jest ważnym elementem zapewniającym niezawodność i bezpieczeństwo. Jego postępowanie jest regulowane przez normy i koniecznie w produkcji i eksploatacji rurociągów.